The parametric model (PM) uses design tools based on structural elements. It allows the developer to define entire classes of shapes, not just specific details. Before the advent of this technology, editing a form was a difficult task. For example, to change a three-dimensional body, the designer had to change the length, width and height. Using PM technology, the designer will need to change only one parameter, the other two are automatically configured.
History of Computer Aided Design
A key milestone in the history of computer-aided design (CAD) was the emergence in 1987 of the Pro / ENGINEER version, now PTC Creo, which introduced the CAD industry to parametric modeling. Since then, this paradigm has been used in almost all major design programs, including SOLIDWORKS, Autodesk Inventor, Creo Parametric, CATIA, NX, and Onshape.
PM design is performed by engineers building three-dimensional geometry in parts. Two-dimensional sketches turn into three-dimensional objects, while design constraints and tolerances are properly implemented in accordance with the design plan. Since each step follows from the previous ones, a detailed preliminary sketch is required.
Despite the power and popularity of RM modeling, another paradigm of direct CAD modeling also has its supporters. Some modern CAD systems use direct rather than parametric modeling based on history; there are also systems that provide a combination of two tools.
Design paradigm and terminology
The parametric design begins with a sketch, and various mathematical functions are used to obtain the final result. The design paradigm first developed by Pro / ENGINEER is called “history-based” because the linear step-by-step nature of the model distinguishes it from direct parametric modeling, which is called “history-free”.
The software remembers the functions in order, and the model performs them step by step. Users often mistakenly believe that only history-based software is parametric. In fact, it includes all models with data, including sizes, samples, wall thickness, diameters, hole depths, and others. Using a parametric approach, engineers can quickly and easily create various structural configurations.
Currently, both parametric and qualimetric modeling have been developed. Qualimetry is a scientific discipline dealing with methods for quantitative determination of the quality of models. This theory, developed in the former USSR by G. Azgaldov, is used today in the development of Russian standards, including in metallurgy and machine processing.
Most of the CAD software allows you to implement high-quality projects. Before making a choice, the developer needs to analyze the indicators:
- The size of the structure.
- The number of developers associated with the project.
- Mobility model.
- The type of file set by the client.
Parametric Modeling Process
Models are built from a set of mathematical formulas and so that they have legitimacy, they must be based on real product information. The perfection of verification methods and the completeness of product information determine the viability of the solution.
There are two popular PM models:
- Structural Solid Geometry (CSG) - defines the model in terms of combining the basic and generated physical forms. She uses logical operations to build a model. This is a combination of three-dimensional elementary forms, for example, a cylinder, cone, prism, rectangle or sphere, which are controlled using simple logical operations.
- Boundary Representation (BR) - A solid model is formed by defining surfaces that form spatial boundaries. Then an object is created by connecting points in space. Many programs use the finite element method (FEM) because it makes it easy to control the internal volume mesh.
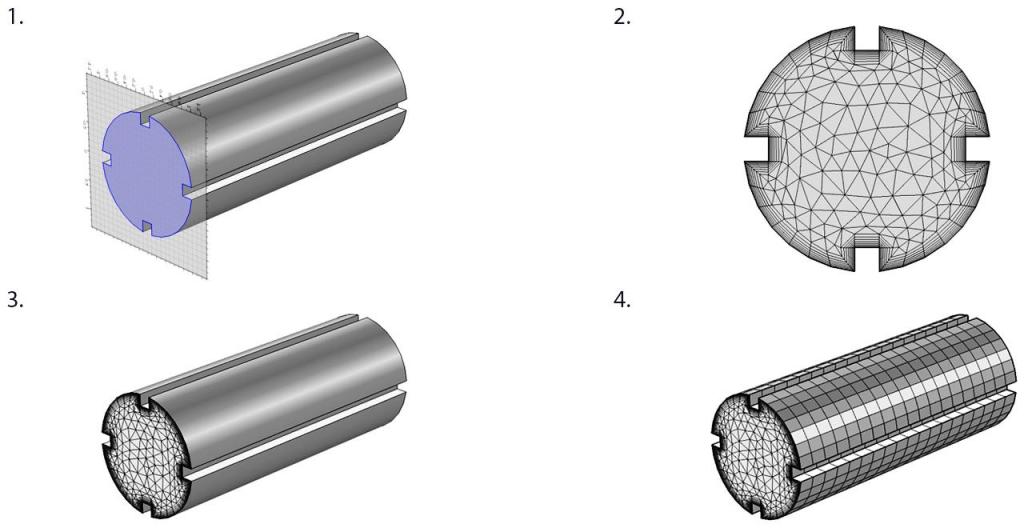
The term parametric 3D modeling means that the MCAD program uses physical data. In this method, dimensions determine the geometry, and not vice versa, as in the case of 2D and traditional three-dimensional solid-state models. Therefore, any editing of values leads to a resizing. In addition, the relationships or constraints used to create product elements are captured and controlled by the program.
Base unit of the project
An element is the basic unit of a parametric solid state model. Just as an assembly includes various parts, a file consists of individual parts. Each function has defining intellectual properties. When constructing an object, geometric constraints and applicable dimensions are indicated. The developer stores these properties in a database and uses to create new products.
Examples of these building blocks, called elements, are openings, ribs, grooves, chamfers and other geometric details. New features depend on existing ones so that design changes are automatically committed. Thus, functional modeling reflects the designer's intention. If a part or related part changes, the software regenerates this characteristic in accordance with the boundary properties assigned to it. For example, an edge defined as tangent to an arc will move to maintain the touch limit if the size of the arc changes.
Computer generated model
In a narrower sense, the term CAD is the computer generation and modification of a geometric model. In a broader sense, it includes all automated actions in the design process: geometric modeling, calculation, collection and provision of information from concept development to manufacturing.
Initially, applications were used to develop production documents. With the increased computing power of a system with sophisticated expert applications and integrated solutions, FEM has become more commonly used for product design and creation. The design of technical solutions is available, thanks to which objects from the very beginning are considered as three-dimensional bodies. If necessary, technical drawings are created automatically from virtual models of parts.
A special advantage of 3D-CAD is the ability to design a product image from any direction. 3D printer allows you to switch from virtual to real object. Along with the detected properties of the material, improved models are created for the given physical properties, for example, strength, elasticity. CAD is used in almost all branches of technology: architecture, civil engineering, mechanical engineering, electrical engineering and such narrow areas as dental technology.
Leading industry software products
There are many parametric modeling programs available on the market today. According to the level of use, they are divided into:
- Low-scale use.
- Wide application.
- Industry Modeling.
The last of these three categories, namely industry software, has gained the most popularity.
Leading industry software products:
- SolidWorks - introduced in 1995 as an inexpensive competitor in the market. SolidWorks parametric modeling software was acquired in 1997 by Dassault Systemes. It is used in mechanical engineering and in the plastic industry.
- CATIA - created by Dassault Systemes in France in the late 1970s. This sophisticated software is widely used in the aviation, automotive, and shipbuilding industries.
- The Siemens NX parametric modeling application, formerly known as Unigraphics, was acquired by McDonnell Douglas in 1977. This is a complete solution for the design and manufacture of products with a wide range of consumption.
- Grasshopper is a parametric design-oriented Rhinoceros plugin that works as a generator of generative algorithms. The advantages of this program are that, unlike many, it does not require scripting experience, it allows you to create circuits from component generation, receiving significant temporary optimization.
- Parametric modeling Compass 3d uses a computer to design objects or systems that function in the real world.
- Autodesk, is an older version of AutoCad and allows you to implement 3D-projects. The scope is industrial mechanics.
- KeyCreator is a non-parametric, non-historical, “direct” 2D / 3D CAD for solid modeling. Originally known as CADKEY, first released in 1984, it runs on DOS, UNIX, and Microsoft Windows operating systems. The first CAD program with 3D capabilities for personal computers. In addition to solid modeling, KeyCreator also performs wireframing and sketching.
Advanced Technology Comparison
SolidWorks dominates enterprise product development, while KeyCreator is the CAD choice for specialized design and manufacturing processes. These are two well-honed tools with clear advantages. To determine if KeyCreator is the right method for parametric modeling, compare which software best suits your needs.
KeyCreator modeling without history allows designers to not only quickly create projects from scratch, but to open and edit any CAD files, regardless of source. KeyCreator has advantages over SolidWorks in the ability to handle unpredictable design changes, and a complete set of translators gives users a tool to do work in any country in the world.
KeyCreator features allow projects to evolve freely, as sketches and 3D models are not bound by operations history or restrictions. This approach allows the initial unstructured concepts to gradually turn into complex assemblies. KeyCreator’s flexible export capabilities mean that 3D geometry easily moves to the next stage of production design.
The PM approach used by SolidWorks is ideal for managing model updates based on product performance characteristics; severe constraints allow you to calculate refinements for structures that are static at this stage. It also provides broad compatibility with data management tools that use design metadata throughout the entire production process.
Cross-platform software for three-dimensional objects
FreeCAD is an open-source designer of cross-platform parametric three-dimensional objects in a cascade. The software is mainly used in mechanical engineering to develop real products. 3D products come with MCAD, CAx, PLM, and CAD, along with a complete package of configuration options and extensions.
Users choose FreeCAD, due to the ease of use based on QT. This software supports and integrates various file formats, you can easily create a three-dimensional figure from 2D, extract design details or adjust dimensions with a sufficient number of components. FreeCAD also comes with an Open Inventor compatible 3D scene rendering model, toolbars, radio buttons, a comprehensive Python API, and layouts.
Features of the program:
- Extensive online documentation.
- Availability for MacOS, Linux, and Windows.
- Comes with a user interface that can be easily customized.
- Provides integrated Python support.
- It provides its users with all the advanced and extensible tools they need: jobs for routes, geographic data, experimental CFDs, finite element analysis (FEA) tools, a robot modeling module, and BIM.
- Supports annotations such as dimensions and text.
- It has many modern features, free for everyone.
Fusion 360 Design Tool
Fusion 360 for Windows is a 3D CAD tool developed by Autodesk. Three-dimensional modeling in the Fusion 360 system is focused on designers and is a powerful tool for developing parts, provides options for testing the functionality of objects and modeling motion. Autodesk Fusion 360 is based on cloud technology. Created data is always stored in the cloud, which facilitates teamwork.
Autodesk Fusion 360 covers the following key factors in product development: functional modeling, rendering, and production preparation. All these functions are combined in one application. Forms work with the T-spline function. By creating smart relationships between components, you can simulate the functionality of assemblies.
The relationship of the individual components with each other is determined by the joints. By adjusting properties such as stiffness or rotation, the components can be positioned with the desired movement relative to each other. To make the product attractive, Fusion 360 has a range of materials that cover the desired surface.
The Autodesk Fusion 360 user interface is well organized. The menu bar provides access to the finished design and the ability to quickly save current projects. In addition, actions can be undone or redone with one click. In the Create section, simple or complex objects are constructed. Design history is accessed through a timeline so that changes can be made and saved.
Modeling starting point
For a sketch object, a two-dimensional model is required, which is then converted in one of the main ways: extrusion, rotation, and sweep.
The starting point for the PM model is a sketch that initially has the exact shape of the part or item being created and is an intelligent representation of the part. It is important to analyze and plan each part before designing in order to determine the most effective sequence of creation.
Unsatisfactory parametric software modeling strategies lead to the appearance of parts, the creation of which will take longer due to complex editing. Designed should be such elements that provide maximum flexibility and product variation, for this, perceiving the finished solid-state model, as a set of changing elements.
Sketch sequence
Before starting to sketch, the model must be studied to determine the best profile for the base case. The best is one that fully describes the overall form, and minimizes the number of remaining functions needed to complete the project. Each new part contains three infinite reference planes, which in space represent the front, top and right planes passing through the origin - the zero point in space.
The general PM procedure is to select the best profile for the first characteristic of the model. Then choose the most suitable plane on which you want to create the first sketch so that the final version has the correct orientation when viewed in graphical form.
Geometry must be created by capturing constraints during sketching and then measured to determine the final geometry. The fully defined variant is black, the incomplete is blue, and the redefined is red.
The 2D sketch is then turned into a 3D solid by extrusion or rotation. It can be turned into solid parts using the scanning process, which has the function of drawing the drawing perpendicular to the plane, and rotating the elements around the axis. This method moves it along a path consisting of straight or curved geometry. For sketching, several sketches are used, with transitions from one figure to another. Each session is associated with a new size. A drawing file with standard dimensions of isometric views is created from the finished solid model.
CAD Benefits
, , , , , , . . , .
, , , .
:
- .
- .
- .
- , .
- .
- , .
- .
- Existing design data can be reused to create new projects.
- Quick design change, increasing efficiency.
- Digital production.
One of the advantages of parametric modeling programs is that they allow you to transfer digital production directly to the project, because it is integrated using numerically controlled machines or 3D printers.